Inspecting Modular Built Homes
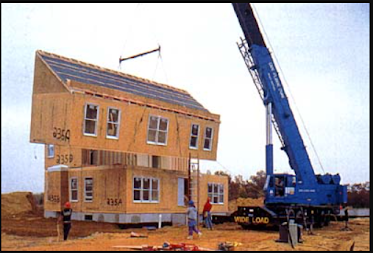
Many people confuse modular homes with manufactured homes. Mobile or manufactured homes are built on steel frames called chassis and they cannot be removed. The chassis are used to support the homes and transport them to their permanent locations. These homes can either be placed in “parks” where other manufactured homes are also placed or be fixed on a permanent foundation, which may qualify them as traditional homes.
Modular homes are built in units that are joined together on-site and, unlike a manufactured home; they can be built as a multiple story house. Modular homes are built with wooden beams that use steel supports which make it possible for the modules to be stacked, allowing the homeowner to have a basement and multiple stories.
Modular homes are built with a process that involves the construction of components in a factory. It starts with a wood frame floor built to attach the wall panels later. The builders will then use fasteners to attach the wall panels. The window openings are already cut out before they are attached. As the structure is built, the drywall, ceilings, plumbing, and electrical wiring are installed under the close supervision of inspectors.
The roof is attached in one of two ways depending on the builder. Some manufacturers will build the roof and then set it on top of the walls. Other companies will send the roof separately and attach it on-site.
The final step is adding the exterior and interior finishes. The buyer can customize their own finishes such as the siding, the cabinets, flooring material, backsplash, vanities, countertops, and many other finishes.
The modular units, are usually shipped with a layer of plastic wrap suitable for transportation purposes only. Failure to erect these assemblies on a timely basis may result in serious weather damage and molded areas. Modular homes are inspected like a “stick built” house; however there are some areas that an inspector should pay close attention to:
– An energy seal should be installed by the factory around the perimeter of the marriage wall.
– To ensure an energy-efficient seal between the modules, a foam gasket or other sealant should be used for this insulating process.
– The perimeter rail of the structure is nailed to the sill plate with 16d nails @ 12” O.C. (For basement sets, all lally columns are located per the recommended schedule and lagged to marriage wall floor rails/girders with four 3/4” x 4” lags each one preferably into each rail. Additional columns are required under each side of marriage wall opening in excess of 52”.)
– The first two modules are bolted together, using 1/2” through-bolts.
– If the home is a two story, the rails of the first floor are bolted together with 1/2” bolts @ 4’ O.C.
– The third module should set on top of the first module, in the same manner as the first. The second floor rails should be fastened to the first floor ceiling rails with 16d nails @ 12” O.C.
– Spray foam is put in place around the marriage wall perimeter.
– Roof center beams must be nailed with a 16d nail @ 8” O.C. in height and 12” O.C. in length, staggered, after leveling the beams to each other.
– Fire stop should be installed in chase areas to assure a maximum of eight feet of vertical distance.
– For an open roof system; fasten truss knee wall to ridge or rafters as per plans.
– Ensure floors are level and not damaged
– The center beams should be bolted together per specifications
– Check factory installed interior / exterior doors for proper working order.
– Drywall cracks, especially at marriage wall openings.
– Check the connection of water lines between modules
– Connection of electric panel to main service and between modules. There may be electrical connection junction boxes where the modules are joined
– Connection of hot water heater to main plumbing pipes.
– Connection of mechanical equipment, furnace, air conditioning, etc., to main systems.
– Ensure there is a bottom sheathing board that completely covers the sill plate
– Examine sheathing splice at marriage wall openings.
– Examine marriage wall doors and cased openings.
Related Articles:
- Inspecting Floor Trusses
- Cantilevered Areas
- Inspecting Structural Insulated Panels (SIPS)
- Inspecting Manufactured Homes
Want To Learn More? Click HERE to Search Our Full Database Of Home Inspector Newsletters.